Rieger Orgelbau, Schwarzach, Austria; Saint Mary’s Basilica, Kraków, Poland
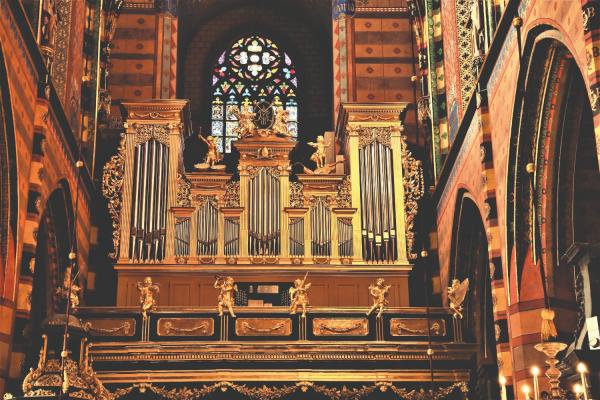
Visitors flock to Kraków. The city, which dates back to the seventh century, was Poland’s capital until the end of the sixteenth century. Left relatively unscathed after World War II and declared a UNESCO World Heritage Site in 1978, Kraków, with its cultural, artistic, and academic heritage from the Gothic, Renaissance, and Baroque periods up to present times, is generally regarded as one of Europe’s most beautiful cities.
The spacious Main Square in the center of the Old Town is flanked by Saint Mary’s Basilica. Built at the end of the thirteenth century, Saint Mary’s is one of the most important architectural structures in Poland and a major destination for pilgrims.
On entering the church, one is almost overwhelmed by the opulence of the interior. Tall stained-glass windows are flanked by monumental murals and crowned with an azure blue, vaulted ceiling, studded with golden stars. One’s eye is immediately drawn to the exquisite late-Medieval high altar, carved by Veit Stoss (1477–1489), and, to its side, but high above, to the Baroque case of the choir organ. On turning around to look back down the nave, the visitor has a fine view of the gilded main organ—with its carved case, sculptured figures, and balustrade entirely covered with gold leaf.
It was Rieger Orgelbau that was commissioned in 2017 to build the new main organ and to rebuild the choir organ. In deference to the church’s extraordinary heritage, the previous historical case forms the middle—i.e., the central and adjacent smaller pipe flats—of the new main organ’s façade. However, Rieger’s highly skilled cabinet makers added the large matching pedal towers and small pipe flats in between (see front cover). Out of respect for our predecessors, several stops from the previous organs were also re-used in both instruments.
The choir organ, with 14 stops on two manuals and pedals, playable both from its own console and from the console of the main organ, was the first to be completed (photo 2, next page, specification below). The main organ, with 62 stops on four manuals and pedal, was inaugurated in 2022.
Tonally, the 76 stops were designed in a romantic-symphonic style with a high range of timbres, an extremely wide dynamic range, and a great degree of stylistic versatility. This versatility is in fact a trademark of Rieger Orgelbau, as it has been since the company was founded in the nineteenth century.
The company
Rieger Orgelbau is one of the world’s oldest organ building companies. Founded in 1843 in Jägerndorf (now known as “Krnov” in the Czech Republic), the company settled in Schwarzach in Vorarlberg, Austria, after the Second World War. Since the beginning, Rieger has built organs in all parts of the world, including the United States—a sampling of the U.S. installations: Bryn Mawr Presbyterian Church, Bryn Mawr, Pennsylvania, III/83, 2005; Pacific Union College, Angwin, California, IV/58, 1980; Nebraska, Union College, Lincoln, Nebraska, III/51, 1984; Christ Episcopal Church, Shaker Heights, Ohio, III/37, 1979.
A characteristic of Rieger is the firm’s very high level of vertical integration, i.e., it produces all the constituent elements of an organ (excluding blowers) itself, starting with the case, wooden pipes, metal reed and flue pipes (from 32′ upwards), windchests and actions, to complete consoles, including keyboards. Even the organ’s electronic controls have been developed and are manufactured in-house. There are currently sixty-two people working at Rieger, making the company one of the largest organbuilding companies in existence.
The Rieger spirit
Since the mid-nineteenth century, there have been many swings in organbuilding style and fashion. Yet, the spirit of Rieger has remained constant: namely, great interest in preserving traditional organbuilding on the one hand, while developing it further with great inventiveness on the other—always subject to the highest quality criteria.
One of Rieger’s strengths lies in thinking through unconventional tasks and then implementing original solutions with maximum precision. The large new organ in the concert hall in Gothenburg, Sweden (IV/112), is an example. Besides a mobile electrical console, a mechanical console was required that can sink below the floor level to save space on the stage. Rieger’s invention can do just that, and yet the mechanical console can be played at any height (photo 4, next page). In addition, the required tonal concept—in the style of late Cavaillé-Coll organs—was expanded with an orchestral division that includes some original Skinner stops from the United States.
A modern façade design was required in the concert hall in Helsinki, Finland (IV/124). The result is a spectacular but unconventional design in which a sculpture, made of functioning curved pipes (Violon 16′) and wind ducts, is positioned in front of the organ’s “general swell” (photo 1, previous page). The inauguration of this organ will take place on January 1, 2024.
Rieger’s spirit has led to its addressing the question of how to transfer the advantages of mechanical actions to electric actions. The firm’s proportional electric action allows one to articulate one’s playing in exactly the same way as on a mechanical tracker action. Even the stop action is proportional: the register sliders can be moved electrically to any position, which can be saved in the combination system that was developed in-house (REA—Rieger Electronic Assistant).
REA makes remote maintenance possible at any time. An organ’s functioning can be analyzed “at a distance” from our headquarters in Austria, and most problems can be addressed and updates made, regardless of where the organ is in the world.
Over the years, the spirit of inventiveness has given Rieger significant influence in shaping the future of organbuilding technology. But for Rieger, organbuilding also includes the past, because respect for and understanding of our predecessors’ work is the foundation for innovation and quality.
Restoration department
It is no wonder, then, that Rieger also has its own restoration department, in which a team of specialists works to renovate, restore, and repair organs, each according to its historical circumstances. Some examples of our work include the restorations of the 1901 Cavaillé-Coll organ in the Tchaikovsky Conservatoire in Moscow (photo 5), the large Georges-Haupt organ in Luxembourg Cathedral, the Kuhn organ in Arbon, Switzerland, and several Anton-Behmann organs in Austria.
When building the new main organ (V/130) in Saint Stephen’s Cathedral in Vienna (photo 3), the aim was to achieve a combination of new work and restoration: the façade was retained, as were the large bellows and around fifty per cent of the pipes. However, the internal mechanisms (inter alia the windchests), the arrangement of the divisions, and half the pipework were built anew. The completely overhauled Rieger choir organ of 1991 (IV/55) was made playable from the new central console, so that 185 stops are available in total. This has resulted in the largest organ in Austria and one of the most important organ installations in Europe.
—Reiner Schuhenn
Rieger Orgelbau GmbH
Main organ
GREAT (Manual I, C–c4)
16′ Principal 61 pipes
8′ Principal 61 pipes
8′ Gedackt 61 pipes
8′ Flûte harm. 61 pipes
8′ Viola da gamba 61 pipes
4′ Octave 61 pipes
4′ Blockflöte 61 pipes
2-2⁄3′ Quinte 61 pipes
2′ Superoctave 61 pipes
2′ Mixtur major V 305 pipes
1-1⁄3′ Mixtur minor IV–V 267 pipes
8′ Cornet V 210 pipes
16′ Trompete 61 pipes
8′ Trompete 61 pipes
POSITIV (Manual II, expressive, C–c4)
16′ Bourdon 61 pipes
8′ Principal 61 pipes
8′ Flauto major 61 pipes
8′ Quintadena 61 pipes
4′ Prestant 61 pipes
4′ Flauto minor 61 pipes
2-2⁄3′ Sesquialtera II 122 pipes
2′ Doublette 61 pipes
1-1⁄3′ Larigot 61 pipes
1′ Scharff IV 244 pipes
8′ Cromorne 61 pipes
8′ Clarinette 61 pipes
Tremulant
Récit (Manual III, expressive, C–c4)
16′ Cor de Chamois 61 pipes
8′ Bourdon 61 pipes
8′ Flûte harm. 61 pipes
8′ Viole 61 pipes
8′ Aéoline 61 pipes
8′ Voix céleste (TC) 49 pipes
4′ Principal 61 pipes
4′ Fugara 61 pipes
4′ Flûte trav. 61 pipes
2-2⁄3′ Nazard 61 pipes
2′ Octavin 61 pipes
1-3⁄5′ Tierce 61 pipes
1′ Piccolo 61 pipes
2-2⁄3′ Fourniture IV–V 281 pipes
16′ Basson 61 pipes
8′ Trompette harm. 61 pipes
8′ Hautbois 61 pipes
4′ Clairon harm. 61 pipes
8′ Voix humaine 61 pipes
Tremolo
SOLO (Manual IV, C–c4)
8′ Tuba episc. 61 pipes
8′ Tuba sonora 61 pipes
8′ Grand Cornet 61 pipes
Campane
PEDAL (C–g1)
32′ Untersatz (ext Majorbass) 12 pipes
16′ Majorbass 32 pipes
16′ Violonbass 32 pipes
16′ Subbass 32 pipes
8′ Principal 32 pipes
8′ Gedackt 32 pipes
8′ Cello 32 pipes
4′ Choralbass 32 pipes
32′ Kontraposaune (ext Posaune) 12 pipes
16′ Posaune (ext Trompete) 12 pipes
16′ Fagott 32 pipes
8′ Trompete 32 pipes
4′ Klarine 32 pipes
Couplers mech.:
II/I, III/II, I/P, II/P, III/P, IV/P
Couplers el.:
I 16, II/I 16, III/I 8, III/I 16, IV/I 8, II 16, III/II 16, IV/II 8, III 16, IV/III 8, IV 4, IV 16
Playing aids
Rieger Electronic Assistant (REA):
20 users with 1,000 combinations with 3 inserts
Title and concert mode
4 Crescendi – adjustable
Sostenuto I, II, III, IV
Sostenuto + I, II, III, IV
Sequencer
Copy function
Repeat function
General cancel
Consoles
Main console (mech.)
Choir stalls console (el.)
Extras
Rieger tuning system
Rieger recording and playback system
Choir organ playable from both consoles
Remote maintenance
Choir organ
MANUAL I (C–c4)
8′ Pryncypał 61 pipes
8′ Amabilis 61 pipes
4′ Octava 61 pipes
4′ Rohrflet 61 pipes
2′ Picolo 61 pipes
2′ Mixtura III 183 pipes
MANUAL II (C–c4)
8′ Pryncypał II 61 pipes
8′ Viola di Gamba 61 pipes
8′ Flet Major 61 pipes
8′ Eolina 61 pipes
4′ Flet Travers 61 pipes
8′ Obój 61 pipes
PEDAL (C–g1)
16′ Subbass 32 pipes
8′ Octavbass 32 pipes
Couplers
II/I, I/P, II/P
Playing aids
Rieger Electronic Assistant
10 Combinations
General cancel
Extras
Can also be played from the main console
Main organ: 62 stops, 84 ranks, 4,492 pipes
Choir organ: 14 stops, 16 ranks, 857 pipes
Cover photo credit: Rieger Orgelbau